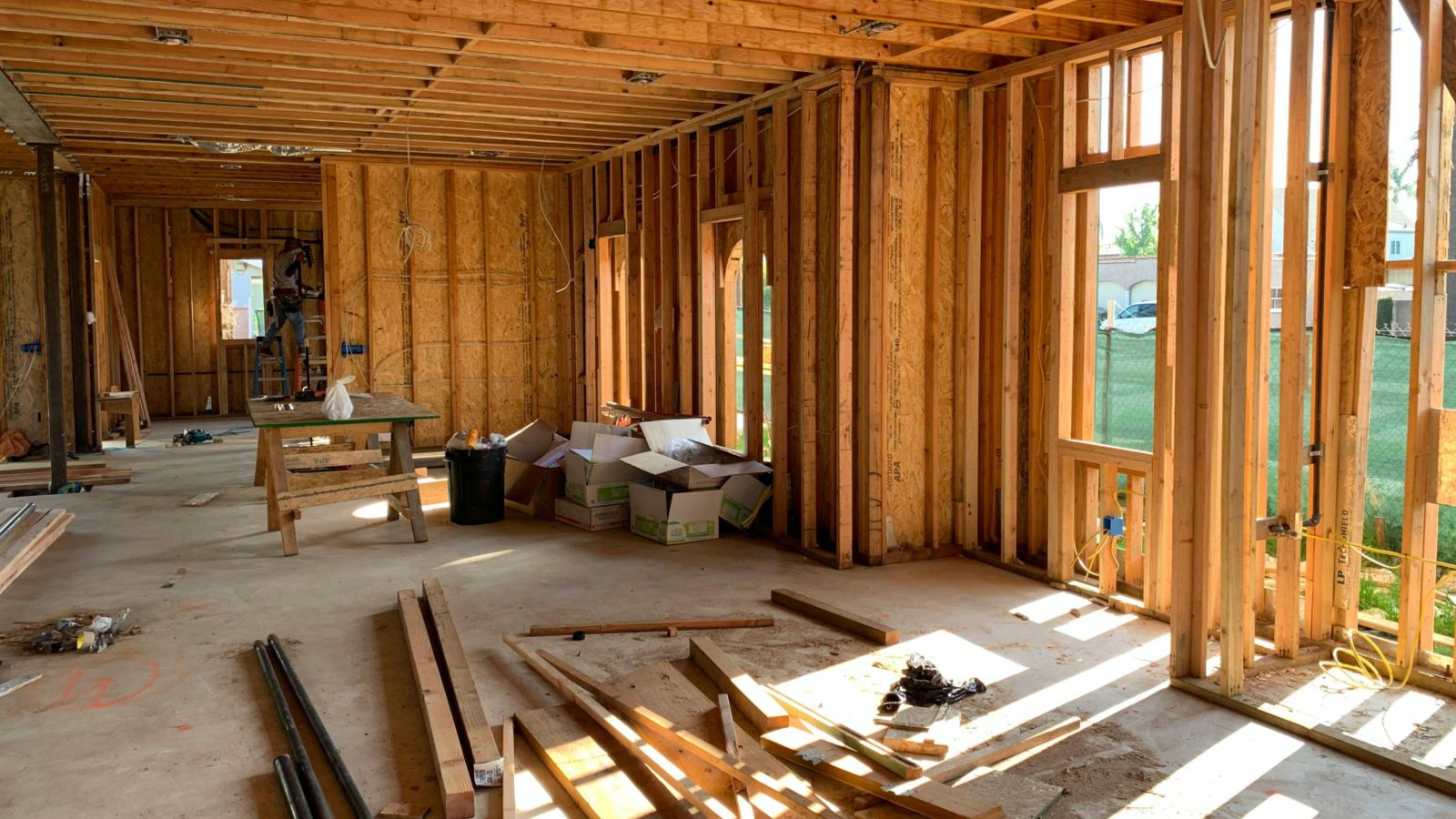
Comment: It’s no secret that many Kiwi homes can be damp and mouldy. But the problem isn’t necessarily restricted to older housing. New houses can also create conditions for condensation and mould—even if they’re designed to comply with the New Zealand Building Code.
Why? The Building Code requirements for managing the indoor environment are relatively basic. Combined with this, we’re using an overly simplistic method to assess and minimise condensation and mould growth on internal surfaces. We need to find a better way to do this to help ensure the new homes we’re building are warm, dry, and healthy.
Shortfalls in the Building Code
Under the Building Code, the method used to assess moisture on the internal surfaces of timber-framed walls and roofs is set out in Acceptable Solution E3/AS1. However, this method fails to adequately consider how thermal bridges influence surface temperature and therefore does not reliably eliminate the risk of condensation and mould.
Thermal bridges are created by building materials that bypass insulation—for example, a timber stud in a wall. Because timber is a less effective insulator, the more thermal bridges in a wall, the greater the influence on surface temperatures, and therefore, the risk of condensation and mould.
The Building Code takes the approach that an R-value (or thermal resistance) of R-1.5 will maintain a surface temperature above the point where mould is likely to grow on internal surfaces. However, this R-value is calculated using the ‘isothermal planes’ method, which simply averages the thermal resistance of timber studs and insulation.
This averaging ignores the effects of timber on surface temperature at localised points. Additionally, it assumes heat flow is one-dimensional and travels only perpendicular to the surface, neglecting heat loss that occurs in other directions at timber junctions.
Compounding the problem, we know that new homes can use significantly more timber framing than may be assumed by designers. More timber framing equals more thermal bridging.
This means that the thermal performance of new timber-framed homes may be below par, increasing the chances of surface condensation, mould growth, and unhealthy living environments.
The hunt for better tools
There is a range of tools available that can calculate conditions on the internal surfaces of a building—and there’s a clear relationship between the complexity of the tool and the reliability of the results. The more time and information required by the tool, the greater the ‘closeness’ of the results to reality.
Ideally, the most detailed tool would be used—but this would likely come with the most cost. In the hunt for a solution, my PhD research compared results from a range of tools to identify how detailed such a tool needs to be to provide a reliable assessment with minimum required time, information, and experience.
My research used measured data from the timber ‘test house’, built by the Building Research Association of New Zealand (BRANZ), to compare results from two main types of building simulation model: a building component simulation (BCS) and a whole building simulation (WBS). Each has its pros and cons. In short, a BCS models a specific component or junction in a building (e.g., a thermal bridge) while a WBS can calculate a home’s internal climate, considering variables such as building orientation, construction, conditioning systems, and ventilation.
Results of this research confirmed that reducing thermal bridging and increasing insulation can lessen the risk of condensation and mould growth, but it cannot eliminate the risk altogether. The other variables that affect the risk, such as heating and ventilation, also need to be considered.
In practice, this means it makes more sense to assess moisture risk using a whole building simulation that calculates internal temperature and relative humidity, rather than focusing on individual components.
Whole building simulations require detailed information about a house to reliably calculate its internal climate. This includes the overall geometry of the building, the properties of materials that make up the construction, as well as good information about ventilation, heating and cooling systems, and how the house is used by the occupants.
The Housing Energy End-use Project 2, conducted by BRANZ, will help here. The project will aid in providing reliable data about the state of the housing stock, including the construction, and heating and cooling systems, and information about how people typically use their home—for example, opening windows to ventilate in summer but not in winter.
Adopting a whole building approach to risk assessment could be used to demonstrate compliance not only with the Building Code’s internal moisture requirements but also with its energy efficiency standard. It could also be used to assess and mitigate the risk of overheating, which is increasingly becoming an issue, especially in apartments.
Whole building modelling could in turn provide a way for designers to improve occupant health, thermal comfort, and energy efficiency with strategies—such as increased insulation—modelled from the initial design stages. This would result in better outcomes than merely meeting the Building Code’s minimum requirements, and potentially lower cost.
This article was originally published on Newsroom.
Griffin Cherrill has a PhD in Building Science from Te Herenga Waka—Victoria University of Wellington. His PhD research was supported by scholarships from Te Herenga Waka and the Building Research Association of New Zealand.